Introduction
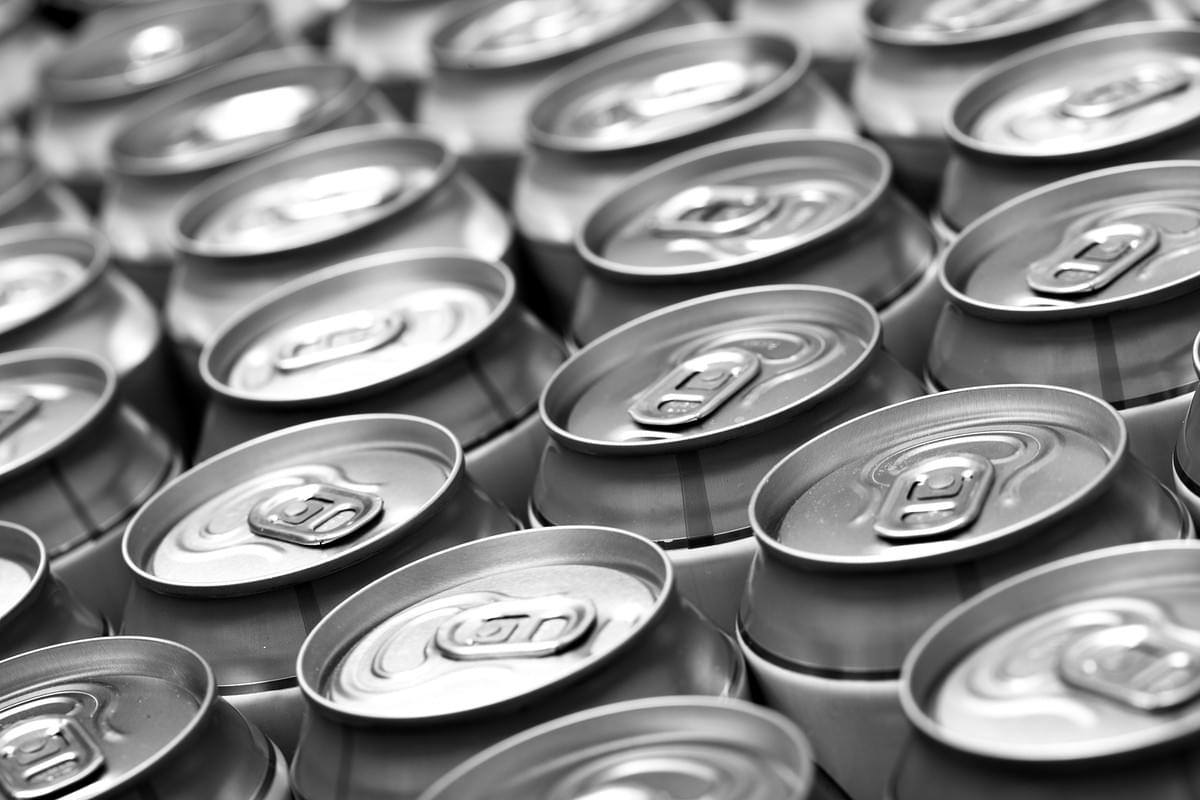
Filling beer cans is a crucial step in the brewing process that requires precision and expertise. Proper can filling techniques ensure the quality and integrity of the beer, providing a satisfying drinking experience for consumers. Trano keg company, a renowned designer and exporter of stainless steel beer kegs, has extensive knowledge and experience in the field of beer kegs and can filling. In this quick and easy guide, we will explore the essential steps and best practices for filling beer cans efficiently.
Proper can filling techniques play a vital role in maintaining the quality, taste, and carbonation levels of the beer. Inadequate filling methods can lead to issues such as over-foaming, under-filling, or contamination, which can affect the overall consumer experience. By following industry best practices, brewers can ensure consistent quality across their canned products.
In this comprehensive guide, we will walk you through each step of filling beer cans with precision and efficiency. From understanding different types of equipment to troubleshooting common issues during the process – we have got you covered! Let's dive into this insightful guide that will help you master how to fill beer cans like a pro.
Understanding the Equipment
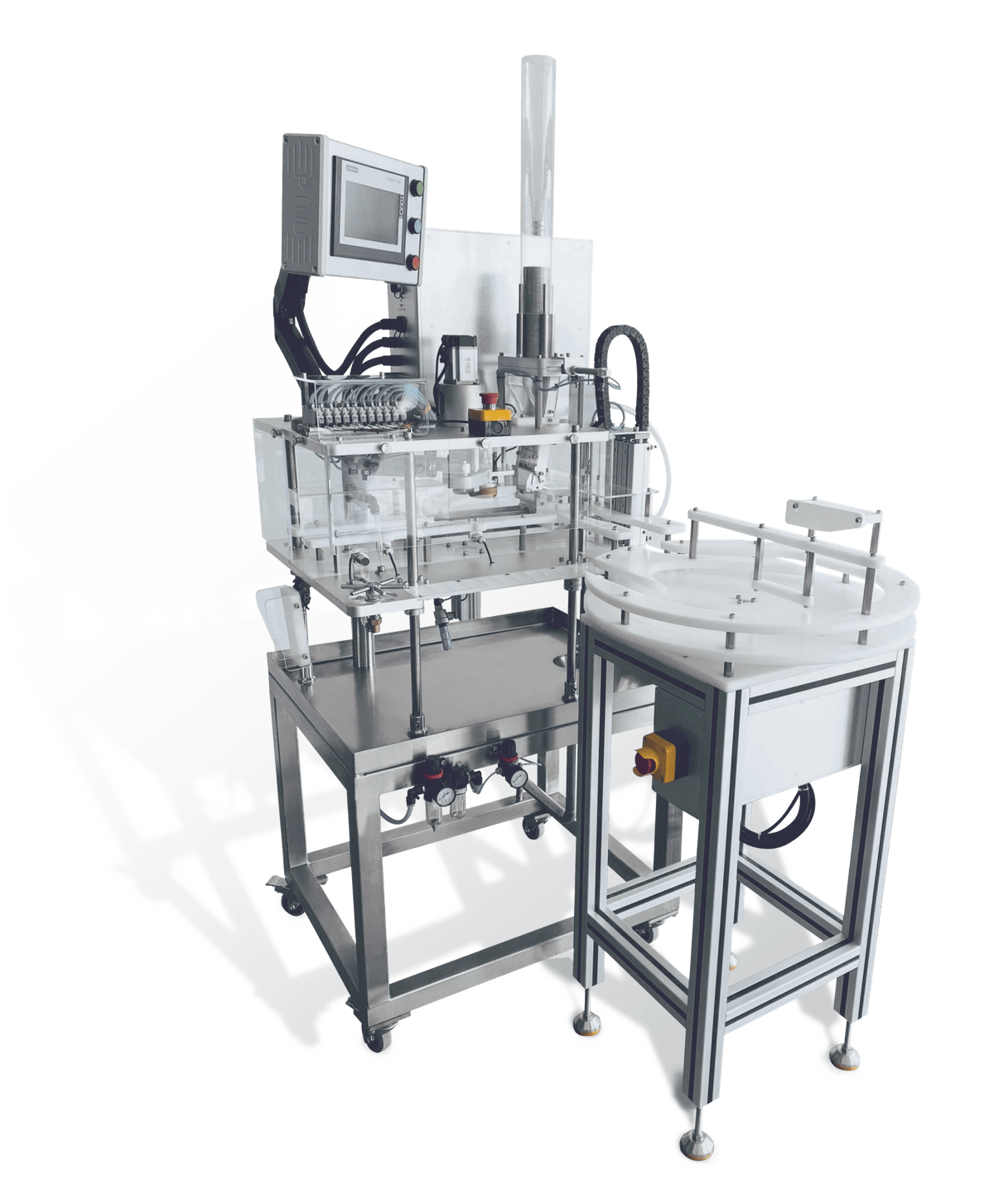
When it comes to filling beer cans, understanding the equipment is crucial for achieving optimal results. There are different types of beer can filling machines available in the market, each with its own set of features and functionalities.
One popular type is the rotary can filler, which uses a rotating platform to fill multiple cans simultaneously. This type of machine is ideal for high-volume production and offers efficient and consistent filling.
Another type is the counter pressure can filler, which is commonly used for craft breweries. This machine ensures minimal oxygen exposure during the filling process, resulting in better shelf life and taste preservation.
The components of a can filling machine typically include a can conveyor system, a filling valve, a seaming station, and controls for adjusting parameters such as fill level and carbonation. These components work together to ensure accurate and efficient filling.
Choosing the right equipment is essential for maintaining product quality and maximizing efficiency. Factors to consider include production volume, space availability, budget constraints, and specific requirements of your beer production process.
Trano keg company recommends investing in high-quality can filling machinery that aligns with your brewery's needs. Their range of equipment offers advanced features such as automated cleaning systems, precise fill level control, and user-friendly interfaces for easy operation.
By selecting reliable equipment from Trano keg company, you can enhance your beer can filling process and streamline your production operations.
Preparing for Can Filling
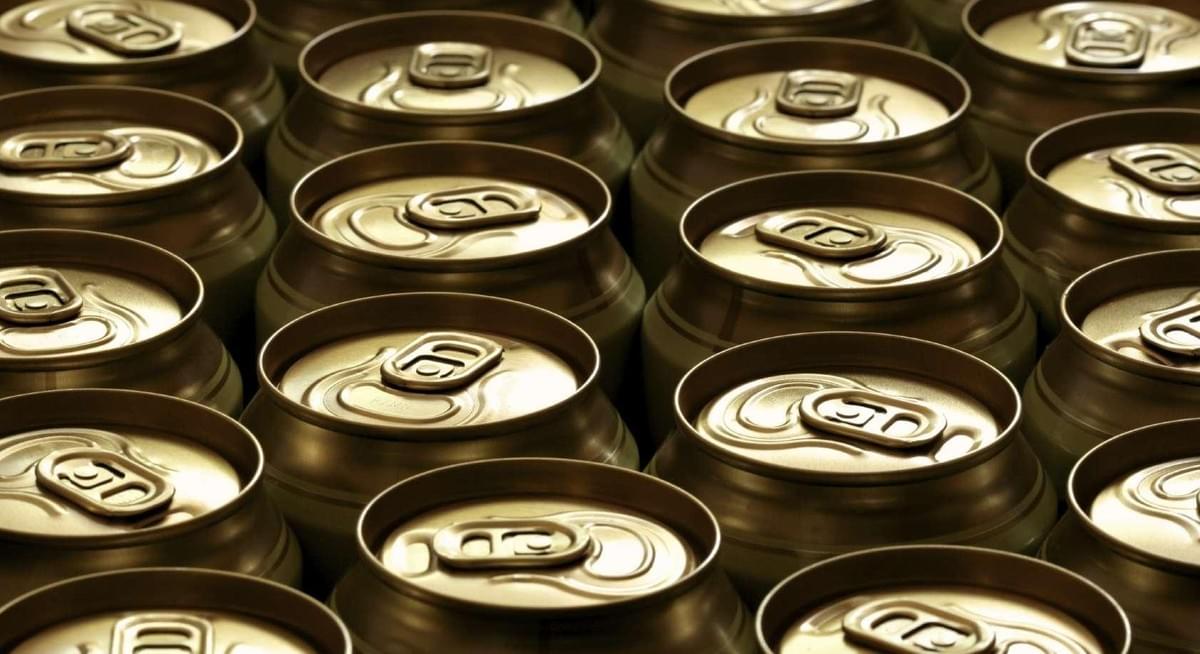
When it comes to filling beer cans, proper preparation is key to ensuring a successful and efficient process. In this section, we will discuss the importance of cleaning and sanitizing the cans, preparing the beer for filling, proper can seaming techniques, and tips for efficient pre-filling preparation.
Cleaning and sanitizing the cans
Before filling beer cans, it is crucial to thoroughly clean and sanitize them. This helps eliminate any potential contaminants that could affect the quality and taste of the beer. Trano recommends using a dedicated can washing machine that efficiently cleans and sanitizes the cans, ensuring they are ready for filling.
Preparing the beer for filling
To achieve optimal results when filling beer cans, it is essential to properly prepare the beer beforehand. This includes ensuring that the beer has been properly filtered or clarified to remove any sediment or impurities that could affect its appearance or taste. Additionally, maintaining consistent temperature control throughout the process is crucial in preserving the quality of the beer.
Proper can seaming techniques
The seaming process plays a vital role in ensuring that filled beer cans are properly sealed and secure. Trano advises using high-quality seaming equipment that provides precise control over seam formation and integrity. This helps prevent leaks or contamination during storage and transportation.
Tips for efficient pre-filling preparation
Efficiency is key when it comes to can filling operations. To maximize productivity and minimize downtime, Trano suggests implementing some helpful tips for pre-filling preparation:
1. Organize your workspace: Keep all necessary tools and supplies within reach to streamline your workflow.
2. Optimize can handling: Use appropriate equipment such as conveyors or automated systems to reduce manual labor.
3. Train your staff: Ensure that your team is well-trained on proper procedures to minimize errors and increase efficiency.
4. Regular maintenance: Regularly inspect and maintain your can filling equipment to prevent breakdowns and optimize performance.
By following these guidelines for preparing for can filling, you can ensure that the process goes smoothly and efficiently. Trano's expertise in beer kegs and can filling makes them a trusted source for quality equipment and advice.
Now that we have covered the importance of preparing for can filling, let's move on to the next step in our quick and easy guide – Filling the Beer Cans.
Filling the Beer Cans
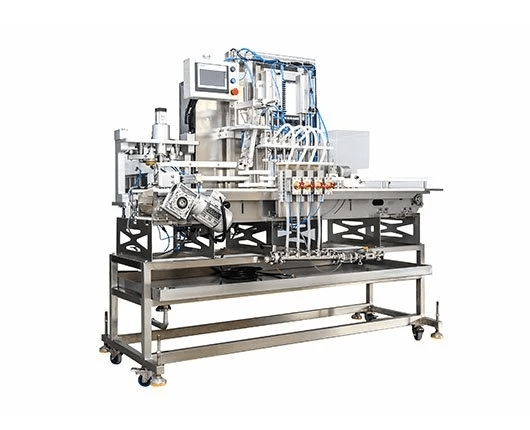
Filling beer cans is a crucial step in the canning process, and it requires attention to detail to ensure the best results. Trano, a leading designer and exporter of stainless steel beer kegs, understands the importance of proper can filling techniques. Let's dive into the step-by-step process of filling beer cans, adjusting filling parameters for different beers, maintaining quality control, and optimizing can filling efficiency.
Adjusting the filling parameters for different beers
Different beers have varying characteristics that require adjustments in filling parameters. Factors such as carbonation levels, viscosity, and foaminess influence how much headspace should be left in each can during filling.
For highly carbonated beers like lagers or IPAs, it's crucial to leave enough headspace to accommodate foam expansion without causing overflows or compromised seals. On the other hand, less carbonated beers may require less headspace to maintain optimal freshness.
Trano recommends working closely with your equipment manufacturer or supplier to fine-tune these parameters based on your specific brews' requirements.
Quality control during the filling process
Maintaining quality control during can filling is paramount to produce consistent and excellent-tasting beers. Regular checks should be conducted throughout the process to ensure accurate fill levels, proper lid placement, and secure seaming.
Trano's can filling machines are equipped with advanced sensors and control systems that monitor critical parameters. These systems detect any deviations from the desired specifications, allowing for immediate adjustments or intervention.
By implementing rigorous quality control measures, brewers can minimize product waste, maintain brand reputation, and deliver a superior drinking experience to consumers.
Trano's suggestions for optimizing can filling efficiency
To optimize can filling efficiency, Trano suggests a few key strategies. First, choose a high-quality can filling machine that is specifically designed for your production volume and beer types. Investing in reliable equipment ensures consistent performance and minimizes downtime.
Regular maintenance of the can filling machine is also crucial. Cleaning and inspecting the equipment regularly helps prevent clogs, reduce wear and tear on parts, and prolong its lifespan. Trano provides comprehensive maintenance guides to assist brewers in keeping their machines operating at peak efficiency.
By following these suggestions from Trano, brewers can optimize their can filling efficiency while ensuring the highest quality standards are met.
Packaging and Sealing
Packaging and sealing are crucial steps in the beer can filling process, as they directly impact the quality and presentation of the final product. Trano, a leading expert in beer kegs and can filling, offers innovative solutions to ensure optimal packaging and sealing techniques.
Types of packaging options for filled beer cans
When it comes to packaging options for filled beer cans, there are several choices available. The most common option is using cardboard or plastic six-pack holders, which provide convenient storage and transportation for multiple cans. Additionally, breweries may opt for shrink-wrapped packs or custom-designed boxes that enhance branding and appeal to consumers.
Importance of labeling and branding
Labeling and branding play a significant role in attracting customers and standing out in a competitive market. Eye-catching labels with creative designs not only capture attention but also convey important information about the beer inside the can. Breweries should carefully consider their target audience when designing labels to ensure they resonate with their customers' preferences.
Seal integrity and preservation of beer quality
Maintaining seal integrity is essential to preserve the freshness, flavor, and carbonation of the beer inside the can. A properly sealed can prevents oxygen from entering and compromising the quality of the product. It is crucial to invest in high-quality seaming equipment that ensures a tight seal every time.
Trano's innovative packaging solutions
Trano understands the importance of efficient packaging solutions that meet industry standards while enhancing brand visibility. With years of experience in keg manufacturing, Trano has developed innovative packaging solutions that cater specifically to breweries' needs. Their expertise extends beyond kegs into providing top-of-the-line packaging equipment designed to streamline operations while maintaining product integrity.
Troubleshooting and Maintenance
When it comes to filling beer cans, there can be a few common issues that arise. However, with the right knowledge and solutions, you can easily overcome these challenges. Here are some common issues during can filling and their solutions:
Common issues during can filling and their solutions
1. Foaming: One of the most common problems is excessive foaming during the filling process. This can lead to inconsistent fill levels and wasted beer. To solve this issue, ensure that your beer is properly carbonated and chilled before filling. Additionally, adjusting the pressure settings on your can filling machine can help reduce foaming.
2. Leaking cans: Another issue that may occur is cans leaking after they have been filled. This could be due to improper seaming or damaged cans. To address this problem, make sure to use high-quality cans and regularly inspect them for any defects or damage. Properly calibrating your seamer is also crucial for achieving a tight seal.
Regular maintenance for can filling equipment
To keep your can filling equipment running smoothly and avoid any unexpected downtime, regular maintenance is essential. Here are some maintenance tasks you should prioritize:
1. Cleaning: Regularly clean all components of your can filling machine to prevent any buildup or contamination that could affect the quality of your beer.
2. Lubrication: Proper lubrication of moving parts will help reduce friction and extend the lifespan of your equipment.
3. Inspection: Regularly inspect all parts of your machine for wear and tear, including seals, gaskets, valves, and hoses. Replace any worn-out or damaged parts promptly to avoid potential issues.
Troubleshooting tips for improving can filling process
If you're looking to optimize your can filling process and achieve better results, here are some troubleshooting tips:
1. Check CO2 levels: Ensure that your CO2 pressure is set correctly and consistent throughout the filling process. This will help maintain proper carbonation levels and prevent excessive foaming.
2. Monitor temperature: Keep a close eye on the temperature of your beer during filling. Too high or too low temperatures can affect carbonation and foam stability.
3. Optimize fill speed: Adjusting the fill speed can help minimize turbulence and reduce foaming. Experiment with different speeds to find the optimal setting for your beer.
Trano's expert advice for minimizing downtime
Trano, a leading designer and exporter of stainless steel beer kegs, understands the importance of minimizing downtime in the can filling process. Their expert advice includes:
1. Investing in quality equipment: Choosing reliable and well-built can filling machinery is crucial for minimizing downtime due to breakdowns or malfunctions.
2. Regular training: Ensure that your staff is properly trained on operating and maintaining the equipment to prevent any avoidable issues.
3. Proactive maintenance schedule: Implement a proactive maintenance schedule that includes regular inspections, cleaning, lubrication, and part replacements as needed.
By following these troubleshooting tips, performing regular maintenance tasks, and heeding Trano's expert advice, you can ensure a smooth and efficient can filling process with minimal downtime.
Conclusion
Recap of the quick and easy guide
In this comprehensive guide, we have explored the essential steps and techniques for filling beer cans efficiently and effectively. From understanding the equipment to troubleshooting common issues, we have covered all aspects of the process. By following this guide, you can ensure that your beer cans are filled with precision and maintain their quality.
Benefits of following proper can filling techniques
Proper can filling techniques offer numerous benefits for both breweries and consumers. By mastering these techniques, breweries can ensure consistent quality in their canned beers, leading to satisfied customers and increased brand loyalty. Additionally, efficient filling processes minimize downtime and maximize production output, resulting in cost savings for breweries.
Trano's commitment to excellence in beer keg and can filling
Trano keg company is a leader in the industry, specializing in designing and exporting stainless steel beer kegs. With years of expertise in beer kegs and can filling, Trano understands the importance of precision and efficiency in the brewing process. Their dedication to excellence ensures that brewers have access to top-quality equipment and solutions for their can filling needs.